Sonochemical coatings
Sonochemistry is based on the application of acoustic energy at appropriate frequencies (from 20 kHz to 2 MHz) to create bubbles within a liquid medium. The bubbles form, grow and then collapse implosively creating small local hotspots, which can reach up to 5000°C and about 200 MPa (2000 atmospheres) in the region previously occupied by the centre of the bubble.
The high temperatures and pressures can break the bonds of molecules and initiate chemical reactions. Moreover, bubbles collapsing near to a surface create micro-scale jets moving at up to 500 m.s–1, which firmly embed nanoparticles of any chemicals formed by the reactions into the surface.
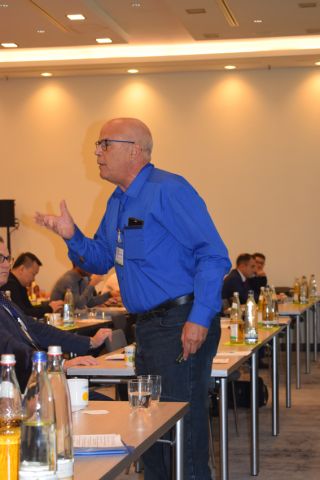
Aharon Gedanken from Bar-Ilan University in Ramat-Gan, Israel, told the conference that the technique can be applied to a range of substrates including textiles, ceramics, polymers, metals, glass, paper and protein microspheres, coating them with inorganic and organic materials to impart a range of properties, such as:
- antibacterial—silver, zinc oxide (ZnO), copper oxide (CuO), magnesium oxide (MgO), thymol, tannic acid and chitosan;
- antiviral—mercaptoethyl sulphonate bonded to silver;
- catalytic—platinum, ruthenium and amylase;
- conductive—silver and gold;
- cosmetic—hyaluronic acid;
- magnetic—iron oxide (FeO);
- optical—rhodamine 6G.
To illustrate the effectiveness of the technique for coating textiles, Gedanken chose a case study involving the development of antibacterial coatings for a range of clothing and bedding in hospitals with the goal of reducing rates of nosocomial infections. Initial work focused on coating polyamide (PA) and polyethylene (PE) fibres with silver nanoparticles (on average 80 nm in diameter). Uniform coatings were applied successfully, but regulatory concerns about the use of silver nanoparticles prompted Gedanken and his co-workers to switch to ZnO and CuO.
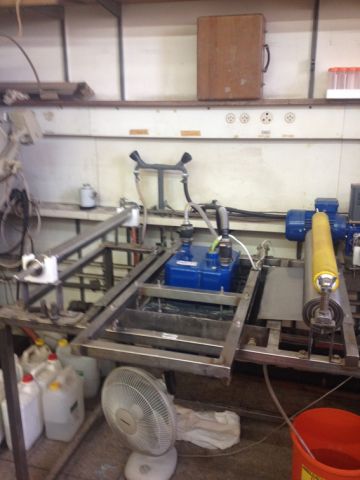
To make the metal oxide nanoparticles, the sonochemical process is applied to zinc or copper acetate in a solution of water and ethanol. This results in hydrolysis and the formation of the nanoparticles and their deposition on the fabric in a single step. In both these cases, the size distributions of the particles were very narrow and the particles were smaller than those of the silver, about 30 nm in the case of ZnO and 10–15 nm for the CuO. After sonochemical treatment, the fibres were observed under a high-resolution scanning electron microscope (HRSEM) to be homogeneously coated.
The group then made bandages using coated and uncoated fibres and determined that the mechanical properties are largely unaffected by the treatment.
Gedanken also showed data concerning the antibacterial effects of CuO coatings on the bandages, which he said were noticeable even at coating weights of just 0.6% by weight (wt%). Compared with uncoated controls, the coated bandages revealed a 100% reduction in the presence after just one hour of gram-negative, Escherichia coli (E. coli), and gram-positive bacteria, Staphylococcus aureus (S. aureus).
This work also resulted in the development of a laboratory-scale, roll-to-roll coating unit and led to the award of funding of about €12 million from the European Union (EU) for a project called SONO, which had the aim of building larger machines. Coordinated by Gedanken, the SONO project involved 17 partners across 10 countries and resulted in the building of two pilot machines: one in Italy that used piezoelectric effects to generate the bubbles; one in Romania based on the magnetostrictive effect. SONO was deemed so successful it won the award as the best project as part of that particular round (FP7) of EU funding.
However, the Italian and Romanian partners raised concerns about the use of the highly volatile and flammable ethanol in a production environment and so the project team decided to use pre-made nanoparticle powders, which were commercially available from Sigma Aldrich of St Louis, Missouri, USA (now called MilliporeSigma as part of Merck of Darmstadt, Germany). They added the nanoparticles to the liquid bath and used the acoustic energy only to embed them in the textile, calling this the throwing stones technique.
The SONO project concluded that there was little if any difference in the antibacterial effectiveness of coatings made by the throwing stones technique and the in-situ formation of either ZnO or CuO nanoparticles. However, the cost of buying commercial nanoparticles was too high and the project reverted to the in-situ method.
In the next stage, tests demonstrated the effectiveness of coated samples using different fabrics (polyester (PES)/cotton and cotton, for instance) against several types of bacteria, including methicillin-resistant Staphylococcus aureus (MRSA), Acinetobacter baumannii (A. baumannii), Enterococcus faecalis (E. faecalis) and Klebsiella pneumoniae (K. pneumoniae). The project also demonstrated that the coatings were resistant to washing under hospital conditions (at 75°C and 92°C). As a result of its solubility, the CuO coating did drop slightly, from 0.9 wt% to 0.74 wt%, after 65 wash cycles at 75°C. Washed in the manner set-out in standard EN ISO 6330/A1/2010, the coated fabric also retains the majority of its effectiveness against Staph. Aureus, Gedanken said, as measured according to the standard EN ISO 20743:2007.
In the final stage, 4000 m of ZnO-coated fabric were made into various garments (such as bedwear for patients) and linen (including pillow cases) for use in a Bulgarian hospital. Compared with the use of the existing textile products, the coated ones reduced the recorded contamination of patients’ throats, backs and bed linen.
To exploit the developments made by the SONO project, Shuki Hershcovich founded a company in 2013 called Nano Textile, which is based in Ramat Gan and employs Gedanken as Vice President of Research and Development (R&D). Its first step was to make the operation of the process fully automatic.
Nano Textile now owns intellectual property rights concerning the reactor used for the process: it has been granted patents in the USA, the EU and Israel, and has patents pending in other strategic markets. The company’s principal focus is on ZnO coatings (ZnO was chosen on the basis of the coatings being white, in contrast with the coloured CuO coatings) for preventing nosocomial infections, but it is also open to exploiting the technology in other areas.
The company has not yet developed a commercial reactor, but when it does it will be based on piezoelectric technology. Nano Textile is also looking to develop a means to create the metal oxide nanoparticles in situ from an aqueous solution to avoid the hazards associated with working with ethanol.
Haptic coatings
A technology developed by Huafeng for creating three-dimensional (3D) coatings was the subject of a presentation by the privately owned Chinese company’s Director of Innovation and RSL Thomas Schmidt. Called Haptic, the trademarked technology aims to exploit the consumer’s attraction to the touch and feel, in addition to any visual appeal, of a product when making a decision to purchase.
Using Haptic technology, Putian-based Huafeng is able to add coatings to selected areas of the substrate (including textiles) and build-up levels to create 3D effects. In addition:
- the levels can be coloured differently to produce visual effects and patterns;
- gloss effects can be applied;
- different perceptions of touch can be added (ranging from soft leather to rough sandpaper).
Summarizing, Schmidt described Haptic as a selective, additive coating technology, the use of which creates value for brands and consumers.
Further, because the coating need only be applied to selected areas, the textile substrate can retain all or largely all of its intrinsic breathability. Nevertheless, the coating also offers protection to the underlying textile, which in some applications allows the use of a lightweight fabric, resulting in improved comfort for the wearer.
To build-up the multiple layers, a base coat (usually transparent) is applied to the fabric. The base coat partially penetrates the fabric, creating a mechanical as well as a chemical bond to the surface. An effect or colour is then applied to the base coat. Generally, subsequent layers each start with another base coating, which adds the necessary thickness to the overall structure where a 3D and/or tactile effect is desired. However, if only colours are being applied, it is possible to dispense with base coatings.
In any case, the layers are applied by automated screen printers, moving along tables up to 60 m long. These machines can apply up to 50 layers to the fabrics on the tables.
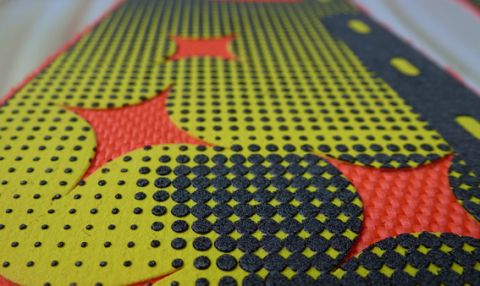
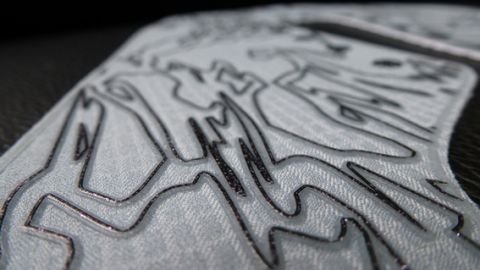
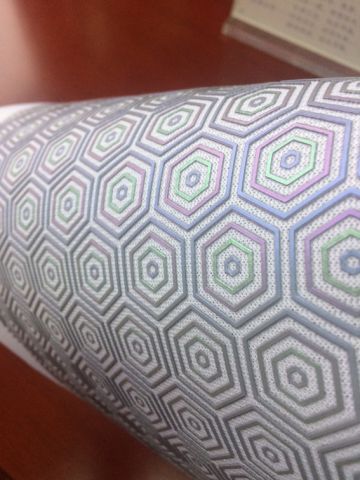
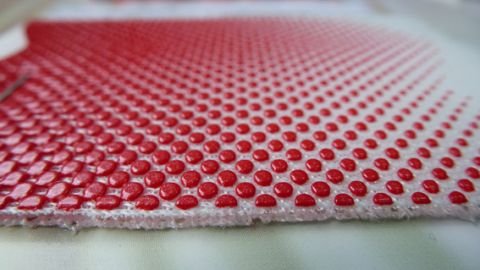
The nature of the manufacturing technology also has other benefits, Schmidt noted. The digital basis of the technology uses raw materials efficiently and keeps waste low. Further, the coating derives from an aqueous solution with a high solids content and so the treated fabric is relatively dry, which helps to save consumption of energy and reduce the number of processing stages, compared with rival techniques, as well as reducing the requirements for labour. The use of water-borne coatings also eliminates the risks to workers associated with the use of volatile solvents (see also, above).
By allowing Huafeng to make an entire component (such as an upper for a shoe), for instance, where previously several suppliers were needed, the technology gives Tier-1 customers a streamlined supply chain, with full accountability for quality and delivery. Customers also benefit from the need for less processing and labour (for instance, the need for sewing is reduced), and can focus on assembly of the final products and logistics.
As a result of the technology’s implementation, Schmidt said that Huafeng, its Tier-1 customers and the brands are developing a new business model for the manufacture of components, with greater interaction between the three parties to fully exploit the new manufacturing and design opportunities Haptic offers.
The principal application so far has been for components (such as uppers) for athletic footwear, with major clients including Nike and adidas. However, other end-uses include apparel, bags, caps and fashion accessories. In apparel, for instance, the ability to coat only selected areas can be used to create additional protection for vulnerable areas of a garment, such as elbow patches.
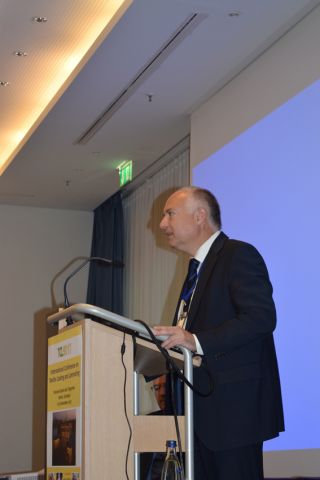
Huafeng began its Haptic production in January 2015, producing enough coated fabric to make about 0.5 million pairs of shoes a month. By January 2017, this had already risen to 2.0 million pairs a month. The majority of Haptic production takes place in Putian, but the company already operates a second small facility in Ho Chi Minh City, Vietnam, where it is investing to expand capacity by 2019. Sales efforts are supported by offices in: Tangerang, Indonesia (a big market for footwear); Portland, Oregon, USA (near to major customers such as Nike and adidas); Herzogenaurach, Germany (near to the headquarters of adidas and Puma; Dongguan, China. The company also has a design centre in Shanghai, China.
Founded in 1999, Huafeng employs about 4800 people, and has an Innovation Center at its new headquarters in Putian, as well as major manufacturing sites dedicated to weaving, knitting, dyeing and digital printing, and finished products. The company’s growth is driving major investments in expansion in all these areas.
Bioengineering polysaccharides
The application of biotechnology to engineer polysaccharides as the basis of a range of high-performance biomaterials was discussed in a paper given by Christian Lenges of DuPont Industrial BioSciences of Wilmington, Delaware, USA.
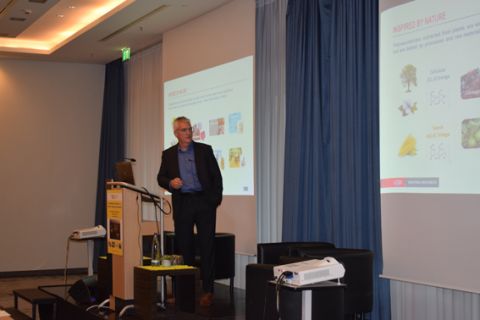
Currently used polymers are derived from petrochemicals, which can be manufactured to a high degree of purity and can be tailored to deliver the precise properties needed for exacting applications. This combination of factors is largely responsible for the commercial success and growing use of polymers in recent decades, he explained. However, increasing demands from legislators and consumers have created a need to find so-called sustainable materials, alternatives that do not exhaust the finite resources of the planet. Ideally, these substitutes should also be recyclable, re-useable, biodegrade after use and create minimal pollution during their manufacture.
A common approach taken in this search has been to extract polymers from plants. However, these extracted materials typically contain many impurities and consist of a variety of structural and chemical forms (they lack homogeneity), features that are not good for manufacturing processes. In addition, the polymers derived from such sources often do not have the high-performance properties of their petrochemically derived counterparts.
The goal of DuPont Industrial BioSciences is to use biotechnology to create polysaccharides that are pure and homogeneous, as well as being derived from sustainable sources. These polysaccharides can then be converted to a variety of industrially relevant derivatives using established chemistry. The resulting materials can be selected and/or chemically tailored to have properties appropriate for the intended end-use; for instance, DuPont Industrial BioSciences has successfully made cationic, anionic, hydrophobic and even thermoplastic polymers.
Lenges stressed that important considerations throughout this work have been to create affordable polymers with high-performance properties and to develop technologies that can be scaled-up to become a realistic part of the materials supply chain, which often requires the production of hundreds, thousands or even millions of kilotonnes a year.
During the five years of the project to date, the approach has focused on the use of sugars as the sustainable raw material, applying biocatalysts (enzymes) to them to produce the polysaccharides. The selection of the enzyme allows DuPont Industrial BioSciences to control typical characteristics of the resulting polysaccharide, including its structure, crystallinity, the size and distribution of its molecular weight, and the nature of the links between the monomers. Controlling the links allows the company to select for certain properties and to determine the resulting polymer’s architecture, linear or branched, which in turn affects the water management characteristics (absorption and retention) that can impact on the wearer’s comfort when applied to textiles.
Glucosyltransferase is one of the enzymes used, Lenges said. This enzyme is produced outside of the cell by several species of bacteria and is part of a unique class that builds-up polymers, rather than breaking them down, in this case working with glucose molecules to make polysaccharides.
Lenges illustrated the extent of progress to date by discussing a specific polysaccharide the company has developed. Using sucrose as the raw material, DuPont Industrial BioSciences has created alpha 1,3-glucan (which has the trademark NuVolve). NuVolve is a water-insoluble free-flowing powder made-up of primary particles each typically 10–30 nm, which aggregate together to form agglomerates of about 1000–5000 nm.
The next steps are to scale-up the processes and to find ways to purify the resulting materials. At present, the processed powder contains about 0.2 wt% or less of residual sugar, a level which needs to be lowered. In addition, production is currently limited to the pilot scale and in 2017 the company made about 30–40 t. During 2018, DuPont Industrial BioSciences has a target to produce 150 t and to supply the first sales of materials to its development partners. It also aims to get management authorization to build the first commercial plant in Europe, which will have a capacity of 20 kt a year and begin operating in 2019 to allow for commercial sales in 2020.
Potential applications include binders for nonwovens. The powder forms stable colloidal dispersions in water, and so can be used in sprays and dispersions for application to the webs. The use of NuVolve also helps to increase the water transport and wicking properties of the fabrics, which is good for nonwovens intended for hygiene applications.
NuVolve can also be used to make effective formulations with aqueous-based latex systems, and so could be the answer to an existing problem. Currently many nonwovens manufacturers will not use latex as a binder, because it adversely affects the ability of the material to wick water. As a result, they sacrifice strength in the fabric. However, manufacturers using latex/NuVolve blends could maintain the adhesion between fibres and so the tensile strength of the nonwoven at the same time as ensuring adequate water-transportation, according to Lenges.
A unique property of NuVolve could also be exploited in such applications. Owing to the bioprocess, the alpha 1,3-glucan is not charged. This contrasts with similar materials made by existing means, such as the Kraft process, which typically impart a negative charge. As a result, colloidal dispersions of NuVolve have a zero zeta potential, which means they form coatings that can be used to effectively transport saline solutions.
Other applications include polyurethane (PU)/NuVolve coatings for polyester (PES) fabrics. Compared with pure PU coatings, treated fabrics have the same resistance to water penetration, a moderately increased breathability (rate of water vapour transmission), a better appearance (high matte finish) and a more natural feel (improved haptics, see also, above).
Finally, DuPont Industrial BioSciences has used formulations in PU/latex systems to apply coatings of NuVolve to leather. In these cases, the matte finishes consistently meet the current benchmarks of the automotive industry, and the addition of the NuVolve improves processing, as well as the stability and haptics of the treated products.